When selecting organic fertilizer equipment, we should pay attention to the annual output, organic raw materials, compost fermentation mode, and the degree of mechanization of the compost turning machine. These are the key factors for organic fertilizer processing. In short, organic fertilizer production is a relatively complex process, but the risk is relatively small. If all aspects are mature, it can bring huge profits to the enterprise. The following describes the difference between organic fertilizer equipment and inorganic fertilizer equipment.
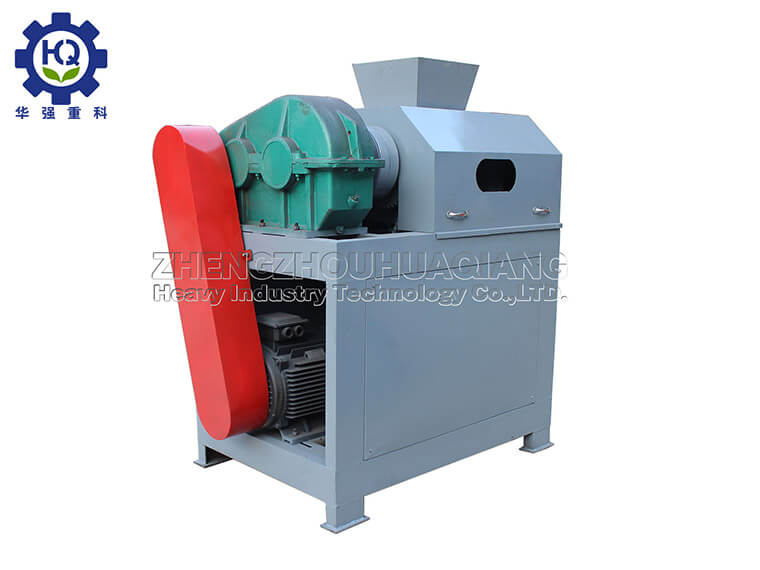