NPK fertilizers are chemical fertilizers. The content of NPK in NPK fertilizers is relatively high. Compared with organic fertilizers, NPK fertilizers are quicker. In modern agriculture, NPK fertilizers are absolutely necessary nutrients point. NPK fertilizers are made from powdered chemical materials containing nitrogen, phosphorus and potassium. Typically, urea, ammonium chloride, calcium nitrate, ammonium sulfate can be used as nitrogen sources. More importantly, phosphorus monoammonium acid, diammonium phosphate, calcium magnesium phosphate and triple superphosphate are commonly used to provide elemental phosphate. In addition, the potassium sources of NPK fertilizers include potassium chloride, potassium salt, potassium sulfate, etc.
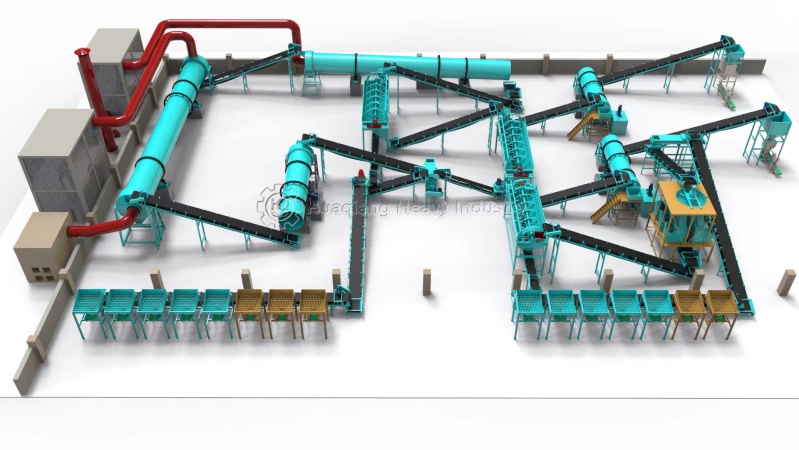
The process flow of the complete set of npk production line equipment can usually be divided into: raw material batching, raw material mixing, raw material granulation, particle drying, particle cooling, particle classification, finished product coating, and final product packaging.NPK fertilizer production line (NPK) is our fertilizer product with stable operation, high quality and easy maintenance and repair. High ball formation rate, less external circulation materials, low comprehensive energy consumption, no pollution, and strong adaptability.
Commonly used granulation equipment for organic fertilizers are: rotary drum granulator, disc granulator, wet granulator, counter-roll extrusion granulator, flat die granulator, and double roller granulator. The selection of the granulator should be determined according to the local fertilizer sales market. In the general granulation process, it is added to the mixer in a specific proportion, and then sent to the drum granulator for granulation after mixing evenly. In the granulator, the material forms a mechanical fluidized bed at a certain rotational speed, during which an appropriate amount of steam is added to provide the corresponding heat and moisture for the granulation process, and then an appropriate amount of circulating washing liquid obtained by the subsequent exhaust gas washing is sprayed to promote the material agglomeration Granulate.